Robust liner hanger enables rotating while circulating for successful installation in challenging formation
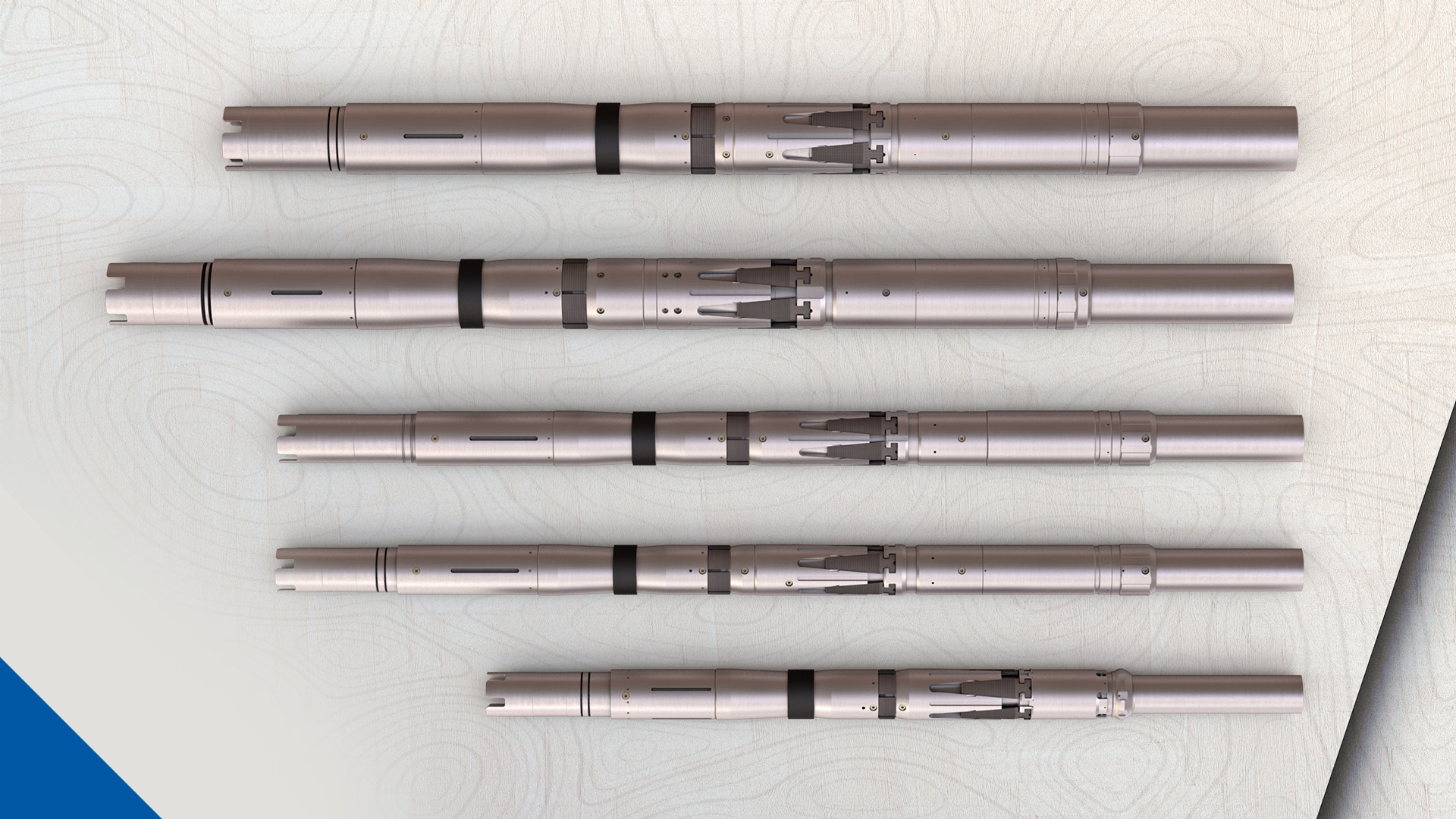
Background
An operator working in Eddy County, New Mexico, implemented a pilot program to maximize the use of hydraulic horsepower during their completions for certain sections of the Lower Wolf Camp formation. The new completion design required heavier casing, which would allow for similar treating pressures of 8,500 psi but enable an increased stimulation rate due to lower pipe friction in the larger casing ID. The Packers Plus PrimeSET® Liner Hanger ensured each system was installed to planned depth, despite high torque and rotation requirements due to well depths and trajectories.
Challenge
The operator’s new completion program increased the intermediate casing size from 7.000-in. to 7.625-in., while maintain a lower completion of 4.5-in. 13.5# liner in a 6.125-in. wellbore. Due to the well depths and trajectories in this area, several installation techniques are used to get the system to bottom, including sliding with slack off, torque and rotation with pumping, and circulation with fluid or gas. These methods require a liner hanger that will not pre-set or release during installation and cause expensive remedial work, as well as lost operational time – and in extreme cases, a lost well.
Solution
The operator had run several PrimeSET Liner Hangers previously as part of its well design and turned to this robust liner hanger again to handle the challenging installation due to well depths and trajectories. The PrimeSET Liner Hanger is deployed using uniquely designed running tools with innovative anti-release features, including a balanced piston that enable the hanger to function in high pressure environments. A torque lock also provides operators with the ability to rotate to bottom, ensuring reliability and performance. Once at planned depth, the PrimeSET Liner Hanger uses premium sealing technology on a single piece mandrel to pack off the annulus and secure the liner in intermediate casing.
Results
To complete the pilot program wells, the operator utilized the 7.625 x 5.5 PrimeSET Liner Hanger directly crossed over to the 4.5-in. liner. During deployment of the systems, wellbore conditions required rotation on two of the systems.
When the systems were between 1,500 and 1,000 ft from bottom (average MD of 22,500 ft), sliding with 20,000 - 40,000 lb of slack off proved to be inefficient at advancing the system. After wellbore circulation provided little or no relief to continue sliding, torque and rotation were used in conjunction with pumping. This method provided limited success and additional measures were required to get each system to bottom.
The next step was wellbore debris removal and the operator required the system remain in rotation during circulation to ensure optimal cuttings removal. Circulation was maintained between 3 and 3.5 bpm for 2.5 hours with 1,000 to 1,200 psi, while the system was rotated at 10 rpm with an average 7,500 ft-lb of torque at surface. Following cuttings removal, the system was rotated with 70,000 lb of slack off to slide to depth. One well required a maximum of 9,500 ft-lb of torque to continue rotation at 10 rpm with the combined 70,000 lb slack off.
All systems successfully reached planned depth and, once at depth, each system was set as designed prior to cementing and displacement operations.
The PrimeSET Liner Hanger is part of the Packers Plus TREX® Cemented Product Line. The TREX line offers solutions such as liner hangers, composite and dissolvable frac plugs, hydraulic toe sleeves and ball-activated sleeves for single point entry or limited entry stimulation. For more information, visit packersplus.com.